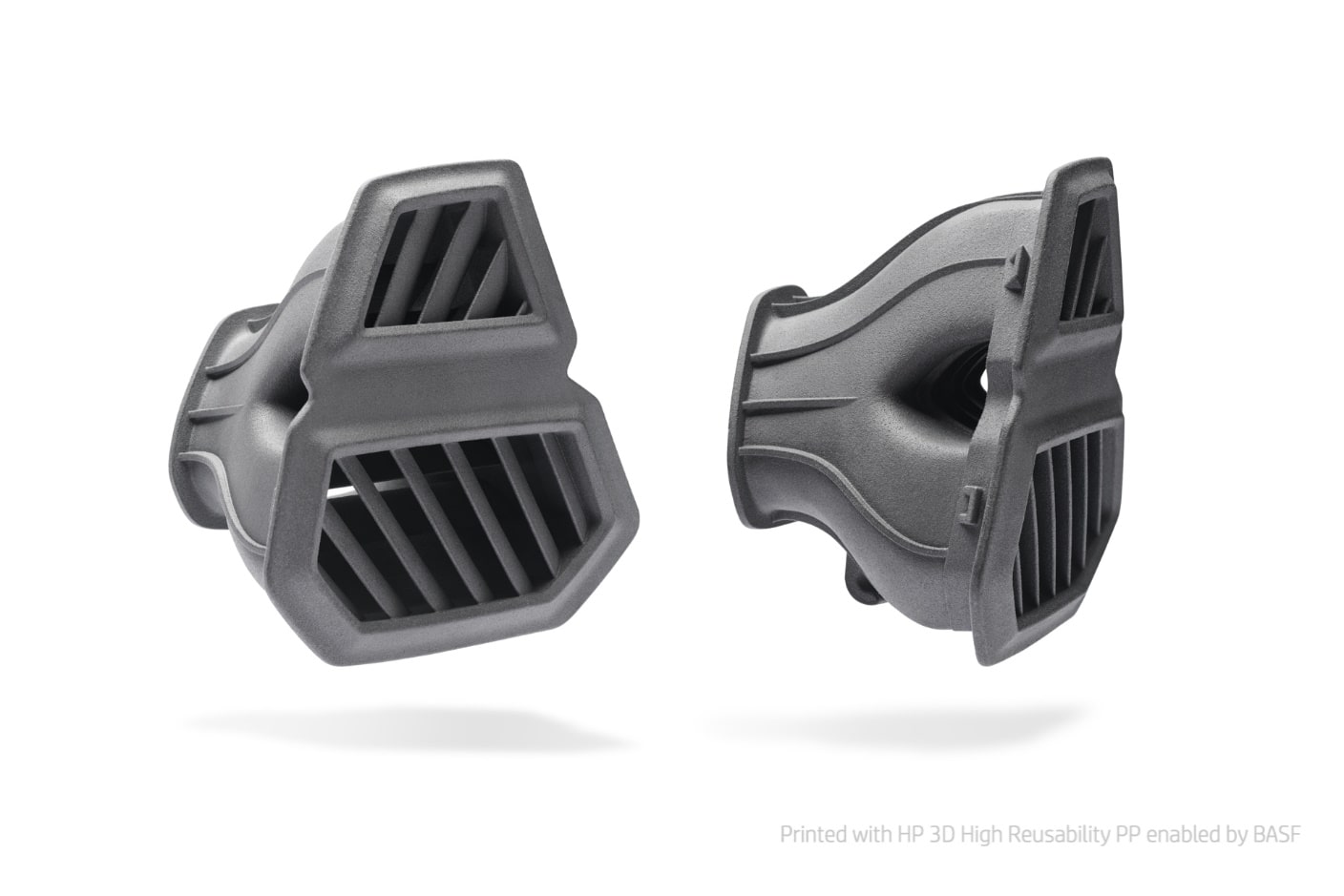
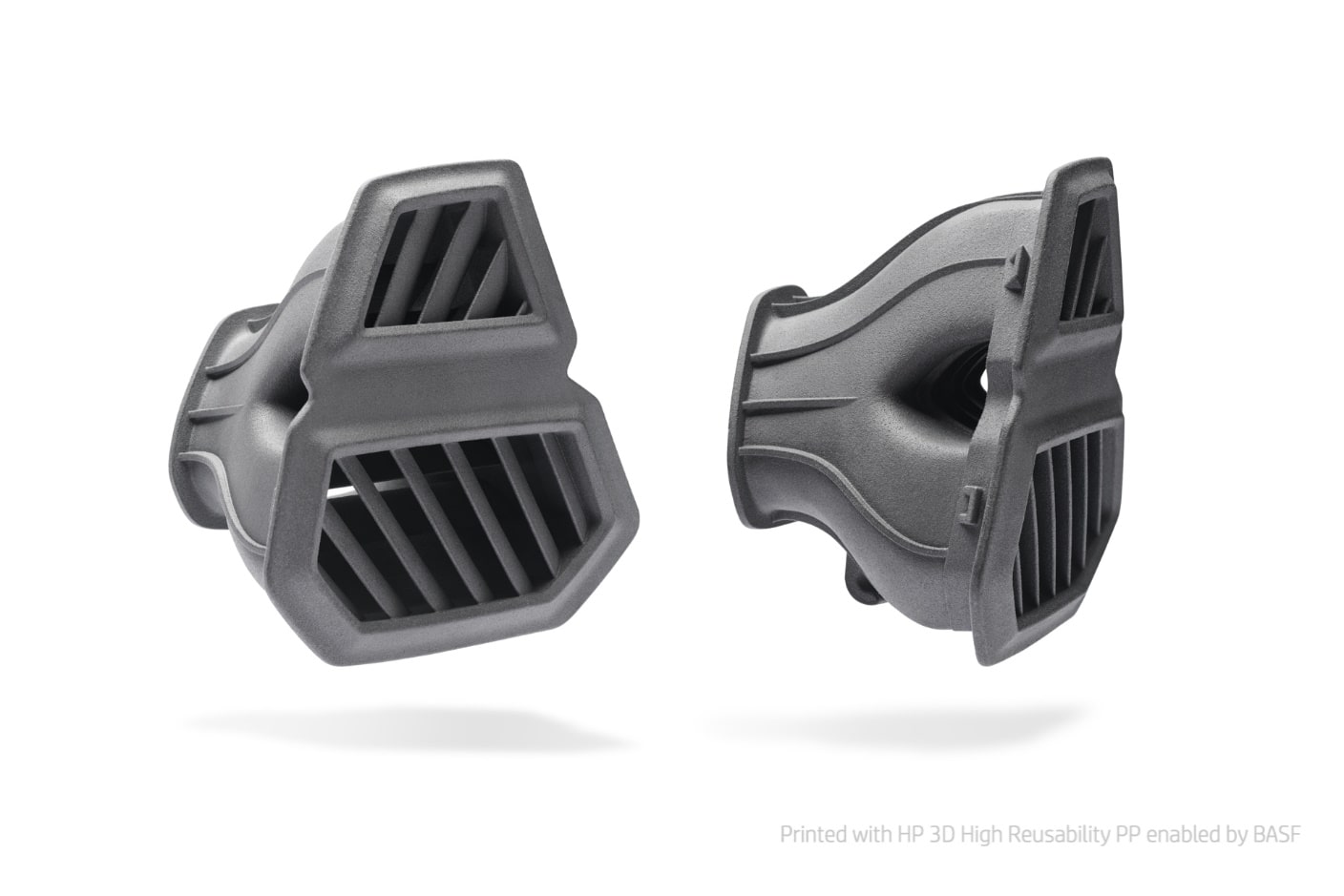
Wprowadzenie i właściwości mechaniczne
Zanim zagłębimy się w szczegółowe wytyczne i zalecenia oraz wartości, opiszemy w skrócie główne właściwości HP 3D HR PP, które są interesujące z punktu widzenia projektantów i inżynierów mechaniki, stosujących ten materiał w przypadku swoich zastosowań.
Temperatura topnienia HP 3D HR PP wynosi ok. 140°C, czyli ok. 40° mniej, niż w dla innych poliamidów HP MJF.
HP 3D HR PP ma przewagę nad PA12 w postaci niskiej wagi, wynikającej z niższej gęstości materiału.
Wydłużenie przy zerwaniu HP 3D HR PP, przypadające pomiędzy wartościami dla PA12 i PA11, zapewnia dobrą plastyczność i wytrzymałość.
Główne właściwości PP dla projektantów części:
- Niska waga
- Elastyczność, plastyczność i wytrzymałość
- Odporność na działanie czynników chemicznych
- Ograniczona absorpcja wilgoci
- Możliwość spawania
Pod względem sztywności HP 3D HR PP również cechuje się dobrym współczynnikiem, jedynie o 12% niższym niż PA12 i PA11.
Pod względem odporności chemicznej i wskaźnika absorpcji wilgoci HP 3D HR PP to jedno z najlepszych tworzyw sztucznych, znacznie lepsze niż poliamidy. Dodatkowo wykazuje bardzo dobre właściwości w zakresie łączenia poprzez spawanie. Tworzywo to można łączyć z innymi formowanymi wtryskowo tworzywami na bazie HP 3D HP PP za pomocą wielu różnych technik.
Objętość umożliwiająca zadrukowanie
Objętość umożliwiająca zadrukowanie to ważna informacja dla projektanta. Chociaż HP 3D HR PP wykorzystuje urządzenie z takim samym wyposażeniem, co urządzenia stosowane do materiałów poliamidowych, maksymalny wymiar Z w komorze drukowania wynosi 370 mm, czyli o 10 mm mniej, z uwagi na wyższą kurczliwość HP 3D HR PP.
Jeśli nie korzystają Państwo z HP SmartStream 3D Build Manager, należy sprawdzić, czy wymiary te są odpowiednio skonfigurowane w programie do przygotowania danego zadania.
Grubość ścianki
Podane tu zalecenia to wartości minimalne ze względów mechanicznych.
Rozdzielczość w osi XY to 20 mikronów, w porównaniu z 80 mikronami w osi Z, dlatego można osiągnąć zalecany przekrój minimalny 0,4 mm w osi XY oraz 0,5 mm w osi Z.
Szczegóły wydruku
Aby uniknąć problemów z częściami oraz osiągnąć najwyższą jakość, należy pamiętać o niektórych specyfikacjach. Minimalne parametry wydruku na płaszczyznach X, Y oraz Z są następujące:
W przypadku liter, cyfr i oznaczeń, obowiązują następujące zalecenia:
Podczas przygotowywania komory roboczej do druku, jeśli to możliwe, elementy wypukłe należy skierować w górę, a wklęsłe w dół.
Elementy montowane po wydruku
W przypadku elementów stykających się z innymi, wartość zapewniająca brak interferencji pomiędzy kołkiem a otworem to 0,3 mm. Jednak w przypadku części, dla których pewna wartość interferencji jest zalecana, bardziej wskazane mogą być wartości 0,1 mm lub 0,2 mm. Zalecamy przeprowadzenie prób przy różnych wartościach.
Jeśli to możliwe, kołek i otwór należy ustawić tak, aby ich oś była prostopadła do płaszczyzny XY, jak widać na poprzedniej ilustracji, co pozwala zapewnić najwyższą dokładność.
Elementy drukowane jako funkcjonalne zespoły
W przypadku części drukowanych jako funkcjonalne zespoły, tak jak poniższy przegub kulowy, minimalny zalecany prześwit pomiędzy licami (w tym przypadku dla promienia) wynosi 1 mm. Jest to oczywiście wartość podstawowa i dopasowanie może być luźne, ale to dobry punkt wyjścia.
Jeśli wymagane jest bardziej ścisłe dopasowanie, ponownie zalecamy przeprowadzenie prób, np. zaczynając od luzu na poziomie 0,3 mm.
Części blokujące
Jedną z zalet MJF w porównaniu z innymi technologiami jest możliwość drukowania bezpośrednio zablokowanych części, takich jak łańcuchy i sieci.
Na niniejszym przykładzie pokazano możliwość drukowania łańcuchów i sieci o różnych geometriach. Należy pamiętać o pozostawieniu zalecanych wartości luzu i odstępu między ogniwami, aby elementy nie połączyły się ze sobą.
Części takie można drukować w stanie złożonym w przestrzeni roboczej komory, np. w położeniu zygzakowym, dzięki czemu mogą być one o wiele dłuższe i większe, niż maksymalna objętość umożliwiająca drukowanie.
Kwestie jakości części: części puste w środku
Rozpraszanie ciepła i kontrola temperatury procesu są trudniejsze w przypadku części o obszernych i masywnych geometriach. Może to spowodować zwiększoną deformację części oraz spadek ich jakości.
W przypadku projektów o masywnych częściach, jednym z najprostszych sposobów zapewnienia jakości części jest ich wydrążenie. To najlepsze podejście w przypadku elementów nieposiadających wysokich wymagań mechanicznych. Czynność wydrążenia części można wykonać automatycznie w CAD i programie do przygotowania zadań.
Z uwagi na to, jak ważne jest unikanie części o dużej masie w przypadku HP 3D HR PP, projektanci muszą przestrzegać określonych wartości stosunku objętości do powierzchni.
Wydrążenie zapewnia dodatkową zaletę w postaci niższych kosztów czynników i materiału. Redukcja kosztów wynika ze zmniejszenia ilości niezbędnego proszku i zastosowanych czynników, które można zredukować aż o 80%.
W przypadku wydrążania części zalecamy minimalną grubość ścianki 2 mm, aby zapewnić odporność konstrukcji. Jeśli chodzi o większe części zaleca się 3 mm.
W przypadku ścianek o grubości powyżej 7 mm lepszym rozwiązaniem może być wzmocnienie części za pomocą struktury zewnętrznej, np. kratownicy.
W każdym przypadku wewnątrz części można pozostawić niespieczony proszek, dzięki czemu będą one cięższe i odporniejsze niż części całkowicie wydrążone.
Mimo że część jest lekka, jest jednocześnie słabsza niż wersja niewydrążona. Różnica wagi wynika z różnych gęstości stopionego i niestopionego materiału.
Projektowanie pod kątem czyszczenia części pustych w środku
W przypadku części wydrążonych, niewykorzystany materiał pozostanie w jej wnętrzu, dlatego wskazane może być wykonanie otworów w celu usunięcia niestopionego proszku.
Zalecamy wykonanie co najmniej dwóch otworów 10 mm po przeciwnych stronach, aby ułatwić oczyszczenie.
Pozostawienie niestopionego proszku wewnątrz części bez żadnych otworów również może być odpowiednią strategią. Nie spowoduje żadnych problemów, a część nadal będzie lżejsza niż lity komponent, gdyż gęstość niewykorzystanego proszku jest niższa niż stopionego materiału.
Struktury lattice (kratownicowe) w druku 3D
Zastosowanie tych struktur polega na wydrążeniu części i zastąpieniu litej masy w jej wnętrzu siateczkową, poprzeczną strukturą zapewniającą wytrzymałość mechaniczną poprzez jednoczesne współdziałanie wielu sztywnych komórek.
Zaletą tej metody jest fakt, że umożliwia zachowanie lepszych właściwości mechanicznych części litej, w porównaniu z częścią wydrążoną, przy jedoczesnym znacznym zmniejszeniu wagi i kosztu części.
Tego typu struktury można też zastosować do zmiany sztywności w niektórych strefach części. Redukcja kosztów wynika ze zmniejszenia ilości niezbędnego proszku i zastosowanych czynników, które można zredukować aż o 60%.
Przeprojektowanie to szybki proces, który można zautomatyzować za pomocą różnych profesjonalnych programów.
Zalecenia dotyczące stosowania:
- Trudno jest podać konkretne zalecenia ułatwiające czyszczenie, takie jak odstęp pomiędzy komórkami, gdyż w dużym stopniu zależy to od rodzaju struktury i jej maksymalnych wymiarów.
- Minimalny zalecany odstęp to 5 mm. Generalnie rzecz biorąc, piramida na bazie sześciościanu z komórkami 8 mm oraz o grubości wiązki 1,2 mm zapewnia dobrą równowagę pomiędzy kosztem i redukcją wagi, właściwościami mechanicznymi i łatwością czyszczenia.
- Ważne jest, aby pamiętać iż w strukturze kratownicowej również może pozostać niestopiony materiał.
Optymalizacja topologiczna i projekt generatywny
Są to dwie podobne techniki umożliwiające redukcję objętości i masy części przy zachowaniu właściwości mechanicznych, Obie są bardzo popularne i zaleca się ich zastosowanie podczas projektowania części HP 3D HR PP.
Najpopularniejsze programy CAD posiadają już moduły oferujące tą funkcję.
W niektórych przypadkach całkowita redukcja wagi może być bardzo duża, co oznacza istotny spadek kosztów.
Zalecamy rozważenie tych technik w konkretnych przypadkach, gdyż mogą one znacząco poprawić jakość części poprzez redukcję ilości stopionego materiału.
Projektowanie kanałów
Podczas projektowania długich geometrii wewnętrznych, usunięcie niestopionego materiału może być trudne. Aby usunąć ten materiał z wąskich kanałów, zaprojektowanie paska lub łańcucha wewnątrz kanału może ułatwić czyszczenie wewnętrzne. Po wydrukowaniu łańcuch można wyciągnąć, aby usunąć większość materiału.
W przypadku kanałów o mniejszej średnicy, czyszczenie można wykonać za pomocą elastycznej śruby lub stalowej linki(np. o grubości 2-3 mm) zamocowanej do standardowej wiertarki.
Części podatne na wypaczenie
PP to tworzywo sztuczne o właściwościach czyniących je wysoce podatnym na wypaczenie. Części płaskie i cienkie są bardziej podatne na zniekształcenia z uwagi na nierównomierne schładzanie, co jest jednym z najważniejszych czynników mogących powodować wypaczanie.
W przypadku zakrzywionych części otwartych, można je łatwo wzmocnić, aby nie zapobiec wypaczeniom, w zależności od grubości i proporcji części.
Części, w przypadku których geometria przekroju jest wysoce zmienna, również mogą schładzać się nierównomiernie. Zasadniczo obszary o większej masie zatrzymują więcej ciepła, i z tego względu stygną wolniej. W obszarach o mniejszej masie krzepnięcie i kurczenie następuje zwykle wcześniej. Różnice w zakresie kurczenia w obrębie jednej części powodują naprężenia wewnętrzne, które mogą spowodować wypaczenie materiału.
Aby zmniejszyć wypaczenia należy w miarę możliwości unikać gwałtownych zmian przekroju, aby zapewnić niski gradient temperatury.
Innym sposobem jest zmniejszenie masy części poprzez jej wydrążenie lub dodanie struktur siateczkowatych [lattice].
Konstrukcje schodkowe
Konstrukcje schodkowe to kolejny waży aspekt, który projektanci muszą wziąć pod uwagę, jeśli istotny jest wygląd i wykończenie powierzchni części.
Multi Jet Fusion to technologia wykorzystująca złoże proszkowe, oparta na technice warstwowej. Obecny profil wydruku HP 3D HR PP pozwala na wytworzenie w komorze roboczej warstwy o grubości 80 mikronów. Warstwy na danej części mogą stać się widoczne gołym okiem, zależnie od ich grubości i orientacji wydruku. Widoczność warstw w przypadku pewnych orientacjach części jest przyczyną zjawiska występowania „schodków”.
Aby mu zapobiec na zakrzywionych lub pochylonych powierzchniach, należy zawsze, o ile jest to możliwe, unikać umieszczania kluczowych powierzchni o niskich kątach wzdłuż poziomej (XY) osi drukowania.
Minimalne wartości zalecane dla uniknięcia wystąpienia konstrukcji schodkowych to:
- 20° dla górnych powierzchni oraz
- 10° dla dolnych powierzchni. Wartość ta jest niższa z uwagi na inne rozpraszanie ciepła w strukturach skierowanych w dół i w górę.
Chodzi o to, by zaprojektować i zorientować część w komorze roboczej w taki sposób, aby kąty te były większe, co zminimalizuje występowanie konstrukcji schodkowych.
Efekt kapilarności
Kapilarność to kolejny aspekt, który musi zostać uwzględniony przez projektantów. Kiedy obszar stopionego materiału chwilowo zmienia się w płyn otoczony przez warstwy niestopionego proszku, jego granice unoszą się wskutek kapilarności. Rezultatem mogą być uniesione i ostrzejsze krawędzie. Kwestia ta wpływa nie tylko na wygląd wrażenia dotykowe, ale też bezpośrednio na wymiary.
Pomiar sprawdzianem wykazuje większą grubość części z kapilarnością w porównaniu ze skanerem 3D lub CMM. Wynika to z faktu, że pomiar taki dotyka najdalszego elementu części o uniesionych krawędziach części. Aby zmniejszyć efekt kapilarności, drukowane elementy należy zorientować tak, aby powierzchnie poziome były przechylone względem osi Z drukarki.
Łączenie części HP 3D HR PP
Istnieją różne techniki i alternatywy pozwalające na spełnienie potrzeb wielu zastosowań za pomocą HP 3D HR PP.
Pasowanie wtłaczane
HP MJF umożliwia użytkownikom drukowanie dopasowanych części, np. wałka i otworu, co pozwala uzyskiwać funkcjonalne zespoły. W zależności od potrzeb funkcjonalnych zespołu, wymagane tolerancje między dopasowanymi częściami mogą być mniejsze lub większe.
Najczęstsze, standardowe typy dopasowania mogą wymagać ściśle określonych tolerancji, np. między IT6 i IT11. Multi Jet Fusion nie potrafi zapewnić tak ścisłych tolerancji, przez co w takich przypadkach zaleca się zaprojektowanie części z dodatkowym materiałem, a następnie ich obrobienie ze ścisłymi tolerancjami (np. za pomocą wiertarki, frezarki lub tokarki, w zależności od ostatecznej geometrii).
W przypadku dopasowanego tłoczenia łożyska kulowego w części wydrukowanej z HP 3D HR PP, należy zaprojektować i wydrukować otwór wstępny co najmniej 1 mm mniejszy od średnicy końcowej, następnie przeprowadzić wiercenie lub obróbkę do osiągnięcia wymaganej średnicy.
Złącza gwintowane: gwinty drukowane
Jeśli istnieje potrzeba zastosowania wkrętów, śrub i nakrętek w celu zmontowania lub przymocowania części HP 3D HR PP, lub pewnych jej komponentów, dobrym rozwiązaniem są złącza gwintowane.
W przypadku średnic o wartości co najmniej 12 mm, można zaprojektować i wydrukować części HP 3D HR PP wraz z gwintem.
Jeśli użytkownik chce zastosować standardowy gwint (np. ISO), gwinty wewnętrzne są rysowane za pomocą CAD, przy tym stosuje się maksymalną dopuszczalną wartość tolerancji z tabeli standardowej, natomiast gwinty zewnętrzne rysowane są z zastosowaniem maksymalnej dopuszczalnej wartości tolerancji z tej tabeli.
W przypadku wartości zarysu gwintu, należy przestrzegać wartości nominalnej.
Gwinty specjalne
Jeśli opracowywane są gwinty indywidualne, należy pamiętać, że trzeba zaprojektować je z luzem na poziomie 0,2 mm do0.4 mm pomiędzy gwintem zewnętrznym i wewnętrznym, przy minimalnym promieniu krawędzi 0,15 mm:
Jeśli to możliwe, zdecydowanie zalecamy wydrukowanie i przetestowanie próbek z różnymi odstępami, aby wybrać najlepszy.
Złącza gwintowane dla rozmiarów poniżej 12 mm
W przypadku gwintów wewnętrznych o mniejszej średnicy, można zastosować dwie opcje:
- Wkręty samogwintujące
Tworzą własny gwint podczas ich wkręcania w część. Wymiary otworu wstępnego są zalecane przez dostawcę wkrętów. - Wewnętrzne gwinty obrabiane
Wydrukować otwór pilotażowy, następnie gwint odpowiednim gwintownikiem. Aby wykonać otwór prowadzący zastosuj wiertło w rozmiarze zalecanym przez dostawcę, lub nieco mniejsze.
Zewnętrzne gwinty obrabiane:
- Najpierw należy wydrukować lity cylinder, następnie gwint za pomocą odpowiedniej narzynki.
- Należy zastosować zalecane średnice cylindra dla tworzyw sztucznych i metali.
Metalowe wkładki gwintowane
Jeśli potrzebne jest np. złącze gwintowane, które będzie wielokrotnie montowane i demontowane z wysoką wydajnością, konieczne może być zastosowanie metalowej wkładki, aby nie uszkodzić gwintu.
Metalowe wkładki to części katalogowe i można podzielić je na 4 różne grupy, jak określono w poniższej tabeli. Najlepsze właściwości mechaniczne zapewniają wkładki montowane poprzez osadzanie termiczne lub wibracje ultradźwiękowe, gdyż materiał wokół nich się topi.
Dostawcy metalowych wkładek zazwyczaj określają średnicę otworu wstępnego oraz wymiary nadlewu, aby zapewnić oczekiwaną wydajność złącza.
Wkładka gwintowa Helicoil
Są to standardowe komponenty, zazwyczaj stosowane do naprawy otworów w metalowych elementach o uszkodzonym gwincie. Przetestowaliśmy je na naszych częściach i działały prawidłowo. Helicoil zajmuje mniej miejsca niż normalna wkładka metalowa. Do instalacji w otworach wstępnych należy zastosować zestaw narzędzi zapewniany przez sprzedawcę.
Klejenie części po wydruku
Jeśli części należy połączyć za pomocą kleju, zaleca się zwiększenie powierzchni klejenia i, o ile umożliwia to grubość, utworzenie jak największej zakładki. Pomiędzy powierzchniami styku należy pozostawić minimalny odstęp 0,2 mm do0,3 mm, w zależności od rodzaju kleju oraz orientacji wydrukowanych części.
Jeśli wymagana jest wysoka precyzja zespołu, zalecamy przeprowadzenie prób z różnymi odstępami.
Spawanie
HP 3D HR PP wykazuje bardzo dobre właściwości spawalnicze. Części można zespawać ze sobą za pomocą różnych metod oraz przyspawać do innych formowanych wtryskowo części PP.
Spawanie punktowe i osadzanie termiczne to potencjalnie najbardziej praktyczne metody spawania części HP 3D HR PP do prototypowania lub produkcji końcowej.
Konstrukcje zatrzaskowe
Zatrzaski to kolejna metoda montażu służąca do łączenia elementów plastikowych poprzez wystający element jednej z części, który odchyla się podczas montażu, wprowadzany w rowek lub w szczelinę w drugiej części. Jest to powszechnie stosowane złącze mechaniczne.
Elastyczność i sztywność HP 3D HR PP powodują, że części dobrze nadają się do tworzenia połączeń zatrzaskowych.
Ponieważ Multi Jet Fusion umożliwia drukowanie wszelkich rodzajów geometrii, połączenia zatrzaskowe można z łatwością stosować do łączenia wydrukowanych części bez konieczności stosowania jakichkolwiek dodatkowych elementów, takich jak śruby i nakrętki.