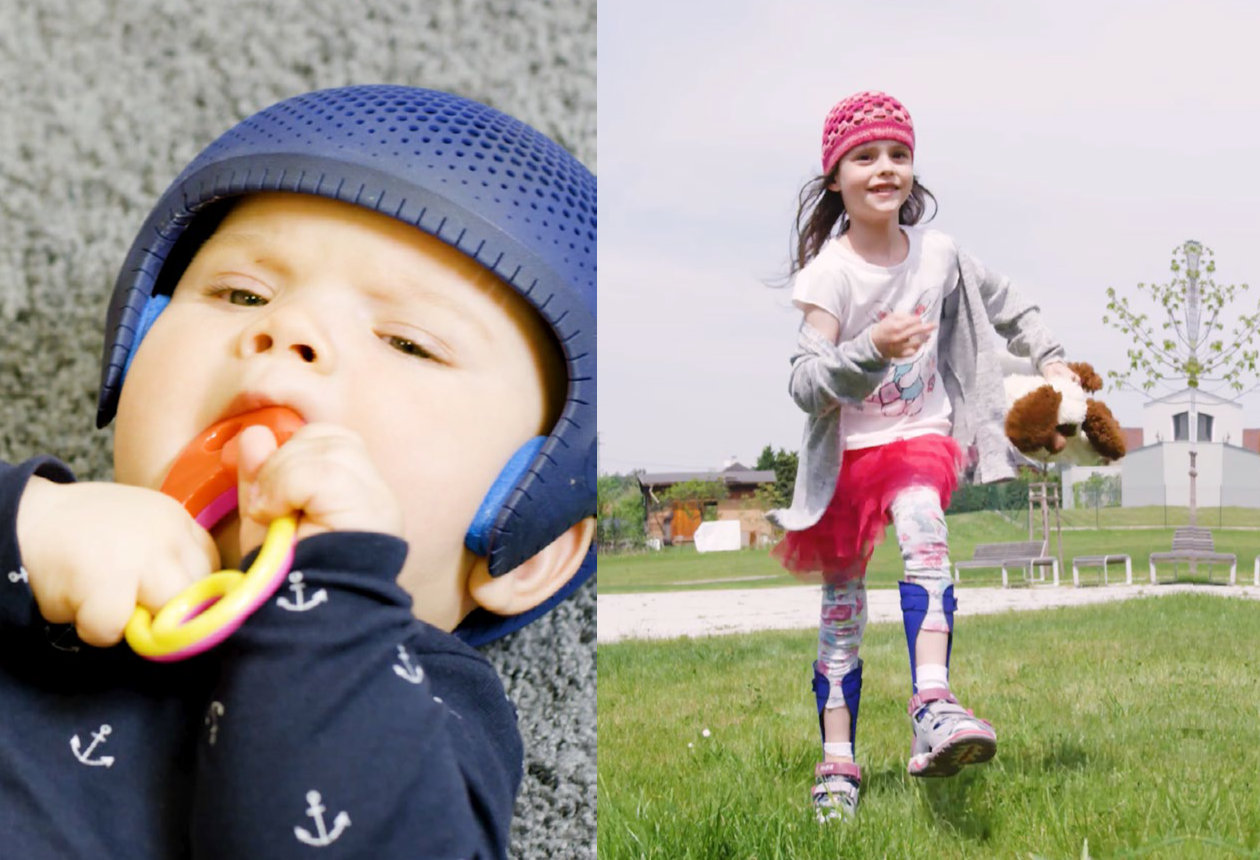
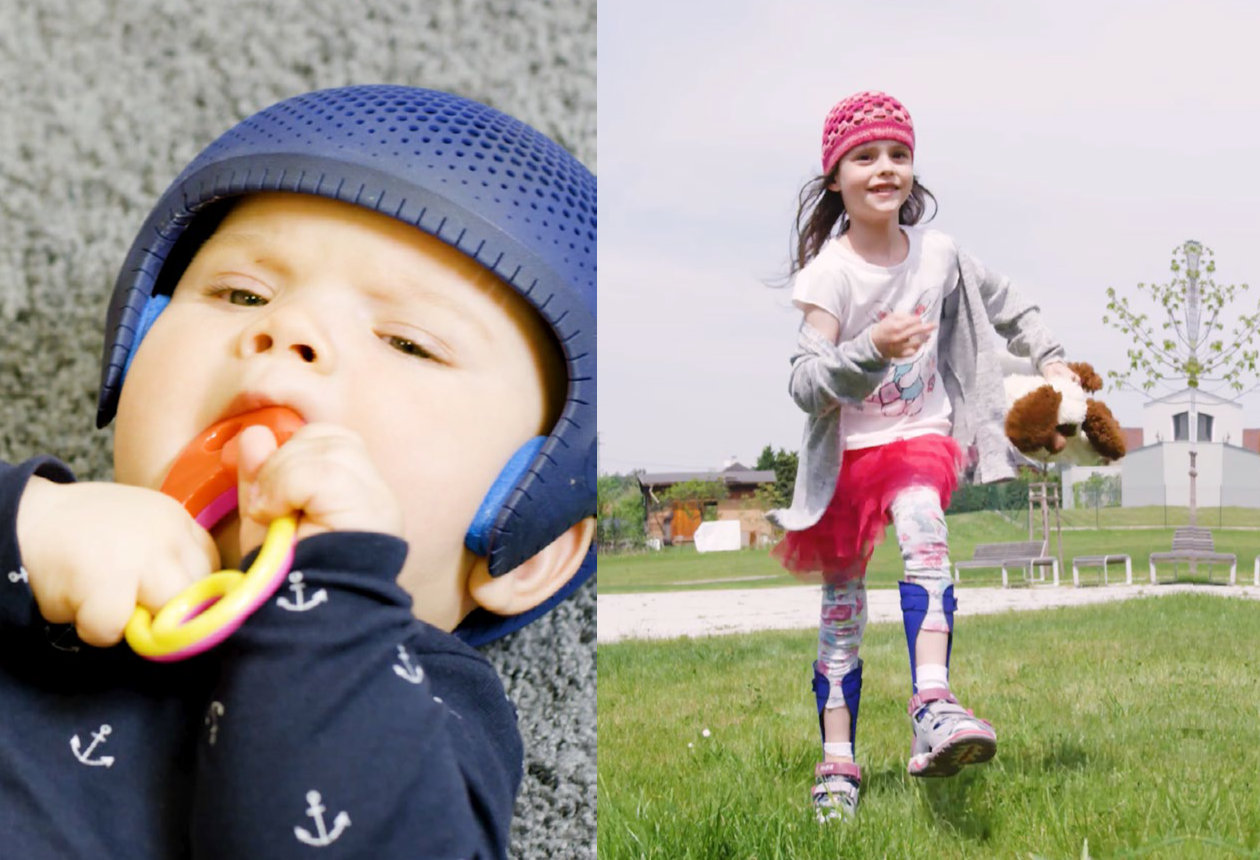
Streszczenie
Branża protetyki i ortotyki (P&O) zbliża się do trudnego okresu, ponieważ liczba urazów sportowych, starzejąca się populacja, przypadki cukrzycy, chorób układu krążenia i amputacji wzrastają każdego roku. Równocześnie spada według Alana Hutchisona, dyrektora generalnego ProsFit, w ciągu ostatnich 10 lat wprowadzono bardzo niewiele zmian w produkcji urządzeń protetycznych i ortotycznych. “Pacjenci mogą zgłaszać dyskomfort podczas noszenia urządzeń, a tylko nieliczni otrzymują odpowiednio dopasowany sprzęt za pierwszym razem, co potencjalnie może wymagać wielu wizyt u klinicystów i ciągłych modyfikacji” – opowiada. “Zwiększona produktywność i stała jakość w produkcji wyrobów protetycznych i ortotycznych to klucze do rozwiązania obecnych ograniczeń mocy produkcyjnych w branży i poprawy jakości życia pacjentów.”
Od lewej do prawej: 8Sole firmy Invent Medical; proteza ręki i orteza nogi firmy Invent Medical; kask firmy Invent Medical; proteza firmy Hulotech
Przyszłość produkcji spersonalizowanych protez i wkładek ortopedycznych
Wdrożenie cyfrowych przepływów pracy w branż protetyki i ortotyki przynosi korzyści w całym łańcuchu wartości poprzez:
- Uproszczenie operacji produkcyjnych i zwiększenie możliwości automatyzacji i jakości produkcji.
- Uwolnienie harmonogramu pracy lekarza, który ma więcej czasu na wizyty u pacjentów, zamiast tracić cenny czas na budowanie form i wprowadzanie zmian przy użyciu tradycyjnie wykonywanych form.
- Podnosi jakość życia pacjenta, zapewniając idealne dopasowanie, lekkość i smukłość urządzenia oraz nowoczesny, wizualny wygląd, atrakcyjny design.
Wykorzystanie druku 3D w produkcji protez i ortez
Z biznesowego punktu widzenia, druk 3D w branży protetyki i ortotyki przynosi niezliczone korzyści w porównaniu z tradycyjną produkcją. W szczególności technologia HP Multi Jet Fusion (MJF) zapewnia dodatkowe korzyści w zakresie precyzji i jakości, prezentując pełen potencjał druku 3D. Skalowalna platforma HP MJF, która obsługuje funkcjonalne prototypy i części końcowe, może przyczynić się do rozwoju biznesu w nowej erze cyfrowej produkcji.
Przejście z produkcji tradycyjnej na cyfrową będzie wymagało od pracowników zapoznania się z trzema nowymi aspektami tej technologii: Skanowanie 3D, projektowanie 3D i druk 3D.
Skanowanie 3D: Każda część ciała może zostać zeskanowana 3D w celu uzyskania cyfrowego obrazu pożądanego obszaru. Proces ten pozwala klinicystom na stworzenie modelu do pracy i/lub przesłanie obrazu bezpośrednio do centralnej firmy zajmującej się wytwarzaniem implantów.
Proces skanowania 3D przez Hulotech
Projekt 3D: Skan jest następnie importowany do branżowego oprogramowania CAD, zazwyczaj Vorum lub Rodin4D. Pozwoli to technikowi na dostosowanie modelu i wprowadzenie zmian, tak jak w przypadku fizycznej formy.
Dostosowany model jest następnie przesyłany do oprogramowania do projektowania 3D, gdzie zespół projektantów i inżynierów tworzy drukowany w 3D aparat ortopedyczny na podstawie zmodyfikowanego skanu 3D. Na rynku dostępna jest szeroka gama narzędzi, z których najpopularniejsze to SolidWorks, Rhinoceros 3D i Autodesk Fusion 360. Ten krok może zająć kilka godzin dla osoby początkującej, lub tylko kilka minut czasu na komputerze dla profesjonalisty, jeśli przepływ pracy został zautomatyzowany.
Po lewej stronie: Hulotech – w trakcie projektowania protezy; Po prawej stronie: Invent Medical projektuje kask ortopedyczny
Drukowanie 3D: Gdy projekt jest gotowy, może zostać wysłany do kolejki druku 3D wraz z partią innych części, które mają zostać wydrukowane jednocześnie. Na przykład, HP Multi Jet Fusion 3D może wyprodukować około 60 par wkładek lub wiele wkładek ortopedycznych (AFO) dla dorosłych w ciągu około 16 godzin, bez nadzoru człowieka.
Po lewej i prawej stronie: Hulotech – Proces drukowania i część końcowa
Tradycyjny przepływ pracy vs. usprawniony przepływ pracy HP 3D
- Tradycyjny przepływ pracy:
- Usprawniony przepływ pracy HP 3D Printing:
Korzyści biznesowe i dla użytkownika końcowego wynikające z zastosowania druku 3D w praktyce
- Przejście od tradycyjnej produkcji do druku 3D wiąże się z przejściem od “sztuki”, w której klinicyści prowadzą papierowe lub mentalne zapisy pomiarów i projektów (i tylko cyfrowe kopie danych pacjenta) do procesu “przemysłowego” o wysokiej powtarzalności i scentralizowanej wiedzy za pośrednictwem dokumentacji elektronicznej, która może przechowywać specyfikacje pacjenta i części.
- Tradycyjne formy są wykonywane przez Protetyka i wielu ekspertów, którzy mogą używać własnych metod, co może prowadzić do niespójnej jakości produktu, podczas gdy urządzenia drukowane 3D produkowane z HP MJF mają stałą, przemysłową jakość części.
- W tradycyjnym procesie produkcyjnym dokonuje się fizycznych pomiarów w celu stworzenia gipsowego odlewu kończyny, a oryginalna geometria może zostać utracona po wielu ręcznych korektach formy, co prowadzi do nieoptymalnego komfortu i estetyki z powodu ograniczeń projektowych i produktowych. Technologia druku 3D pozwala jednak na stworzenie trójwymiarowego modelu cyfrowego , który może być zachowany do celów porównawczych i wspomagania przyszłego leczenia. Innowacyjne możliwości projektowania dostępne dzięki drukowi 3D zmieniają protetykę i wkładki ortopedyczne w spersonalizowane produkty konsumenckie.
- W przypadku tradycyjnej produkcji mamy do czynienia z dwuetapowym procesem, w którym klinicysta zazwyczaj dopasowuje urządzenie testowe do pacjenta, a następnie wykańcza je, dokonując pewnych korekt; optymalizacja wymaga pracy ręcznej i wielu wizyt. Druk 3D wymaga tylko jednoetapowego procesu, ponieważ optymalizacja następuje przed rozpoczęciem produkcji, zapewniając właściwe dopasowanie za pierwszym razem.
Jak druk 3D zrewolucjonizuje branżę
Zastosowanie druku 3D to nie tylko stworzenie bardziej efektywnego przepływu pracy, ale także możliwość ponownego przemyślenia sposobu funkcjonowania, działania i wyglądu produktów protetycznych i ortotycznych.
Sukcesy firm z tej branży są napędzane przez innowacje, a zatem poprzez inwestowanie w badania, rozwój i wdrażanie technologii. Przy włączaniu druku 3D do procesów roboczych, konieczne są również inwestycje w projektowanie i inżynierię produktu, jak również świeże spojrzenie na projektowanie.
Druk 3D ma moc przekształcenia protetyki i ortotyki w przemysł dóbr konsumpcyjnych bez ponoszenia dodatkowych kosztów. Dzięki zastosowaniu zasad projektowania wytwarzania addytywnego, konstrukcja i wydajność wyrobów może zostać znacznie poprawiona. Niektóre z najbardziej istotnych strategii, które należy rozważyć przy drukowaniu 3D tego typu wyrobów obejmują:
- Zmienna struktura ścian: Dzięki ściankom o zmiennej grubości , które mogą być generowane za pomocą druku 3D, projektanci i producenci mogą kontrolować sztywność i wytrzymałość w każdym aspekcie końcowego wyrobu. Dzięki temu specjaliści mogą tworzyć znacznie lżejsze urządzenia o większej sztywności w miejscach wymagających wsparcia i większej elastyczności w innych obszarach, co poprawia komfort użytkowania. W wielu przypadkach druk 3D pozwala na tworzenie urządzeń, które są cieńsze niż ich termoplastyczne lub wykonane z włókna węglowego odpowiedniki. Dostosowana do potrzeb sztywność, mniejsza waga i zwiększony ogólny komfort prowadzą do większego zadowolenia pacjenta i potencjalnie lepszych wyników leczenia.
Drukowana w 3D orteza na stopę i nogę od firmy Crispin Orthotics
- Zaawansowane struktury: Specyficzne cechy projektu, takie jak siatki (sieć przekrojów poprzecznych) i oczka mogą modyfikować wydajność i właściwości materiału części poprzez zwiększenie sztywności, zmniejszenie wagi i poprawę oddychalności. Te struktury i wzory, które są możliwe do osiągnięcia tylko dzięki technologii druku 3D, wpływają na zachowanie materiału poprzez projektowanie.
Kask drukowany w 3D przez Invent Medical
- Konsolidacja części: Dzięki naturze druku 3D, części i mechanizmy mogą być drukowane jednocześnie poprzez zazębianie się ruchomych elementów i łączenie skomplikowanych kształtów. Konsolidacja części zazwyczaj zmniejsza wagę, redukuje zakres prac montażowych i koniecznych przeróbek oraz eliminuje zależność od kilku dostawców.
Drukowane w 3D ortezy na stopy od Crispin Orthotics
- Branding i personalizacja: Druk 3D pozwala klinicystom i producentom na personalizację produktów za pomocą logo lub nazwy firmy. Ponadto ułatwia znakowanie elementów numerem zlecenia produkcyjnego w celu cyfrowego śledzenia ich cyklu życia.
Drukowana w 3D 8Sole (wkładka) firmy Invent Medical
Dlaczego technologia HP Multi Jet Fusion?
Druk 3D z wykorzystaniem technologii HP Multi Jet Fusion to niezliczone korzyści dla producentów, lekarzy i pacjentów, w tym:
- Właściwości materiału. Stała jakość materiałów klasy przemysłowej stosowanych w technologii HP Multi Jet Fusion (MJF) (takich jak HP 3D High Reusability [HR] PA 11) zapewnia doskonałą odporność na uderzenia i plastyczność, i zwiększone wydłużenie przy zerwaniu. Ponadto wybrane materiały HP 3D przeszły pozytywnie badania pod kątem działania drażniącego i uczulającego na skórę; dlatego wyroby wykonane z tych materiałów, w podobnych warunkach, spełniają wymogi zgodności z USP klasa I-VI i wytycznymi FDA dla Intact Skin Surface Devices [urządzenia niepowodujące naruszenia powierzchni skóry].
- Właściwości izotropowe. HP MJF jest idealnym rozwiązaniem do produkcji wyrobów ortotycznych i protetycznych, ponieważ dzięki zastosowaniu w procesie druku specjalnych czynników zespalających może zapewnić podwyższone właściwości izotropowe.
- Zoptymalizowana wydajność. Wytwarzanie większej liczby części dziennie dzięki ciągłem u drukowaniu.
- Trwałość i oszczędność kosztów. Drukowanie przy użyciu technologii HP MJF może zminimalizować ilość odpadów dzięki wiodącej w branży możliwości ponownego wykorzystania proszku. Ponadto, w przeciwieństwie do procesów wytwarzania odejmującego, takich jak obróbka CNC, HP MJF (proces wytwarzania addytywnego ) wykorzystuje tylko dokładny materiał wymagany do “zbudowania” urządzenia. Na przykład w przypadku produkcji wkładek do butów może to skutkować 97% redukcją odpadów materiałowych.
- HP MJF pozwala na konsolidację sprzętu w rozwiązanie typu “wszystko w jednym”. To skalowalne rozwiązanie oferuje optymalny stosunek liczby operatorów do liczby maszyn i może prowadzić do nawet 8-krotnego skrócenia czasu pracy ręcznej.
Zastosowanie technologii HP MJF w praktyce
Od czasu wprowadzenia technologii HP MJF, pionierzy na obszarze protetyki i ortotyki czerpią korzyści, jakie druk 3D może przynieść ich własnym procesom produkcyjnym.
Wkładki ortopedyczne Crispin
Crispin Orthotics dostarcza rozwiązania i produkty ortopedyczne dla Narodowej Służby Zdrowia, jak również dla pacjentów prywatnych w Wielkiej Brytanii i całej Europie.
Dzięki technologii HP Multi Jet Fusion, firma Crispin eksperymentowała ze złożonymi geometriami, aby produkować bardziej efektywne i nowocześniej wyglądające urządzenia dla pacjentów, takie jak ortezy stawu skokowego i stopy (AFO). Stwierdzono również, że koszt produkcji z HP MJF jest o 50% niższy w porównaniu z włóknem węglowym.
“Branża wkładek ortopedycznych ma tendencję do dość tradycyjnej produkcji” – mówi Mark Thaxter, dyrektor zarządzający Crispin Orthotics. “Druk 3D pozwala na tworzenie produktów, których wcześniej nie byliśmy w stanie wytworzyć.”
Kołnierz ortopedyczny firmy Crispin Orthotics
OT4
OT4 Orthopädietechnik GmbH, z siedzibą w Monachium, w Niemczech, opracowuje, projektuje i produkuje ortezy dostosowane do potrzeb pacjenta przy użyciu technologii druku 3D.
OT4 przeszła na technologię HP MJF pod kątem produkcji swojego kasku, dynamicznej ortezy stawu skokowego (DAFO) oraz ortezy ręki. Dzięki technologii HP MJF, OT4 jest teraz w stanie sprzedawać produkty bez konieczności stosowania kosztownego obrabiania wyrobów po ich wytworzeniu.
“Konstrukcja 3D z wykorzystaniem HP Multi Jet Fusion umożliwia wytwarzanie zupełnie nowych produktów o funkcjonalności, która do tej pory nie była możliwa” – mówi Andreas Flamm, CEO OT4. “Zanim HP weszło na rynek z tą nową technologią, nie mogliśmy dostarczyć produktu o takiej samej trwałości, takiej samej jakości i w takim samym czasie.”
Orteza ręki z OT4
Invent Medical
Firma Invent Medical przeszła od produkcji z wykorzystaniem procesów subtrakcyjnych do technologii HP Multi Jet Fusion, aby produkować wkładki ortopedyczne na zamówienie. Klinicyści mogą wykonać trójwymiarowe skany części ciała i przesłać je na stronę internetową firmy Invent Medical, gdzie dokonują wyboru i dostosowują produkt końcowy, który ma być wydrukowany w 3D.
“Dzięki HP Multi Jet Fusion jesteśmy w stanie zaprojektować i bezpośrednio wydrukować produkt końcowy” – mówi główny projektant firmy Invent Medical, Ales Grygar. “To pozwala nam dostarczać urządzenia ortopedyczne o wyższej wydajności, które są lżejsze, bardziej elasty czne i wygodniejsze.”
Technologia HP Multi Jet Fusion pomogła stworzyć więź między pacjentem, opiekunem i producentem sprzętu medycznego oraz umożliwiła firmie Invent Medical rozwinąć swój model na skalę globalną.
Orteza stawu skokowego i stopy firmy Invent Medical
ProsFit
ProsFit jest międzynarodowym liderem w dostarczaniu protez poniżej kolana drukowanych w 3D w oparciu o przemysłowe rozwiązanie o gwarantowanej jakości, które dostarcza klinikom na całym świecie oprogramowanie dla klinicystów do tworzenia solidnych i niezawodnych protez.
Technologia HP Multi Jet Fusion pozwala na w pełni cyfrowe rozwiązanie typu “od skanu do druku”, “wirtualizując” projektowanie i dopasowywanie ortez, oraz zwiększając wydajność co najmniej pięciokrotnie. Ortezy ProsFit Original są sprzedawane w UE jako wyroby medyczne wykonywane na zamówienie, zawsze według projektu i specyfikacji protetyka.
“ProsFit jest pierwszą firmą w branży protetycznej, która o pracowała w pełni cyfrowe rozwiązanie do projektowania i produkcji ortez protetycznych” – mówi Alan Hutchison, dyrektor generalny ProsFit. “Widzimy, że rola HP jest bardzo duża w naszej branży… i posiadanie dostępu do tego spr zętu, o którym wiemy, że jest spójny i wysokiej jakości, będzie dawało duże korzyści.”
Proteza nogi firmy ProsFit