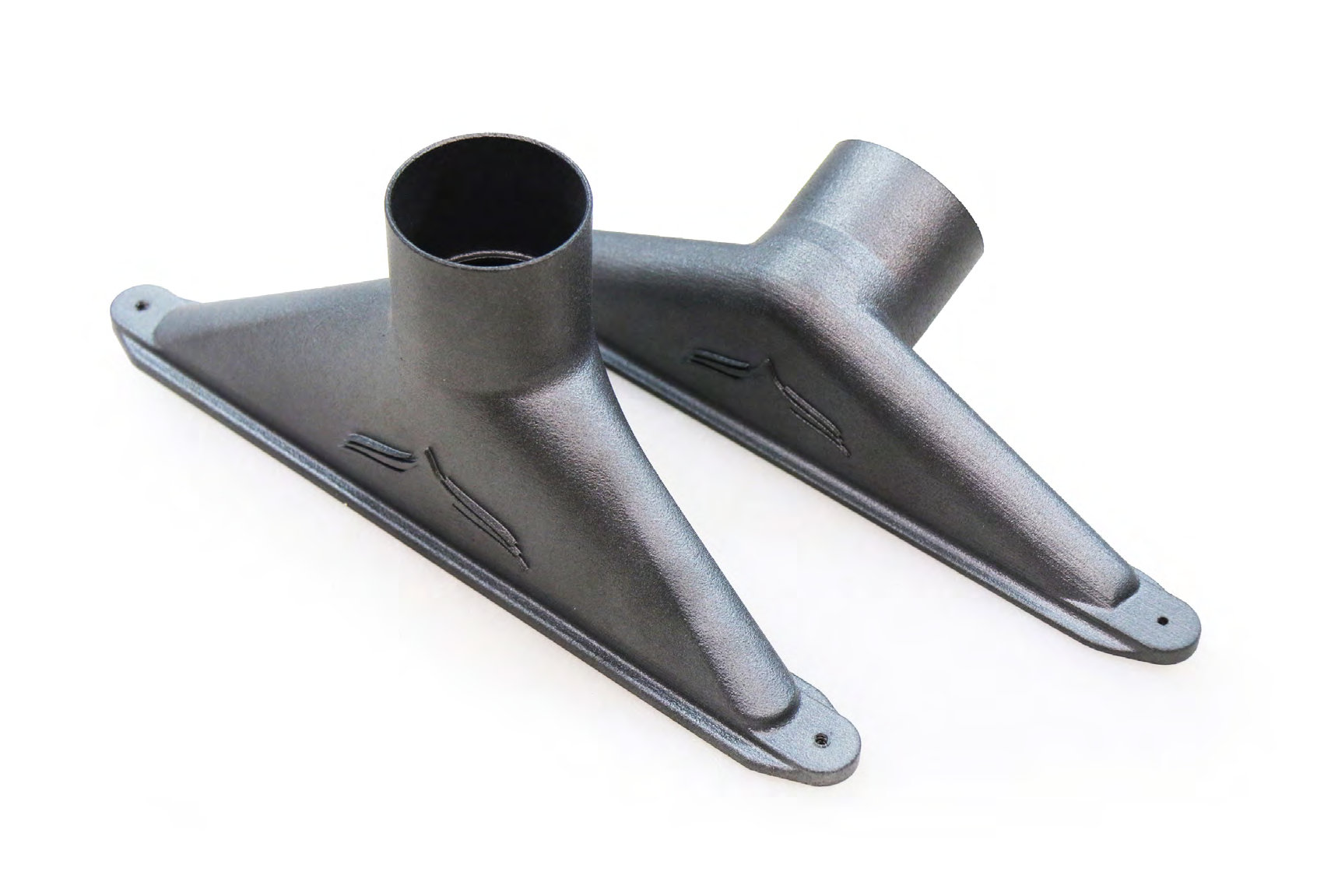
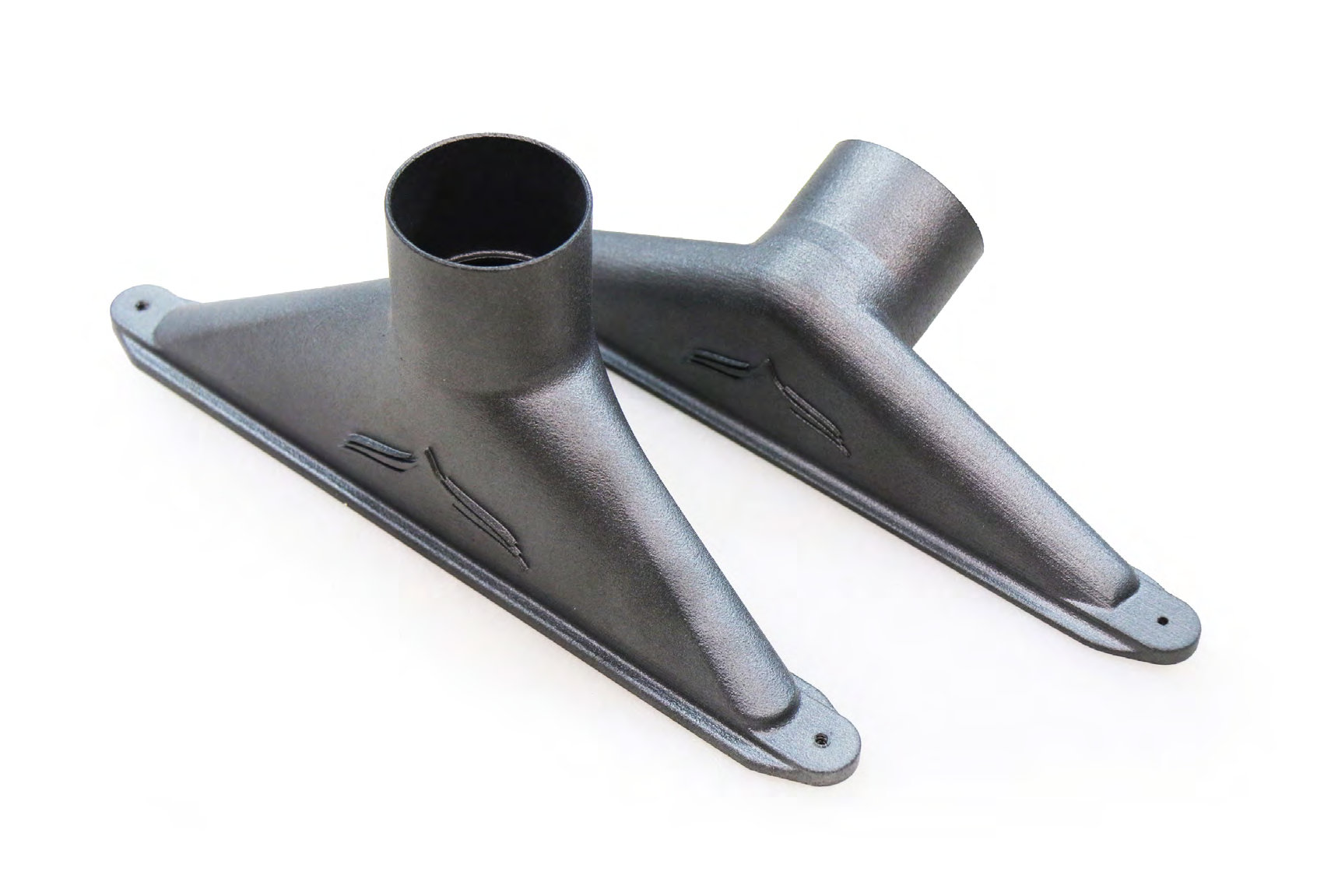
Specjalista w dziedzinie klasycznych samochodów, firma Eagle, musiała znaleźć sposób na wytwarzanie małych ilości elementów do Jaguara E-Type po niższych kosztach – ale w najwyższym standardzie.
- Branża
Renowacja klasycznych samochodów - Sektor
Drukowanie prototypów i elementów - Cel
Redukcja kosztów ogólnych małych wolumenów części przy zachowaniu jakości - Podejście
Wykorzystanie wiodącej na świecie technologii druku 3D do produkcji elementów klasycznych samochodów, wystarczająco trwałych i atrakcyjnych dla grupy kolekcjonerów Eagle - Technologia | Rozwiązanie
HP Jet Fusion 4200 Industrial, 3D Printing Solution - Materiał
HP 3D High Reusability PA 11, HP 3D High Reusability PA 12, HP 3D High Reusability PA 12 Glass Beads, ESTANE® 3D TPU M95A
Wstęp
Powstały w 1961 E-Type wytwarzany był do roku 1975. Jest to jeden z klasycznych samochodów sportowych. Cieszy się przez to bardzo dużym zainteresowaniem kolekcjonerów. Eagle E-Types to wiodący, brytyjski restaurator klasycznych, sportowych Jaguarów E-type.
Firma pieczołowicie odtwarza każdy zdobyty samochód, co zajmuje około 4 000 godzin. Każdy E-type jest też ulepszany zgodnie z nowoczesnymi standardami jakości, przy jednoczesnym zachowaniu stylu i etosu pierwotnego projektu. W emitowanym przez BBC programie Top Gear Eagle E-Type nazwano „prawdopodobnie najlepszym, wytwarzanym ręcznie samochodem świata.”
Jednak firma napotkała wyzwanie. Musiała znaleźć sposób na wytwarzanie specjalistycznych części w małych ilościach, bez ponoszenia zaporowych kosztów związanych ze zmianą oprzyrządowania. W dużych procesach przemysłowych, zaprojektowanych pod kątem o wiele większych serii produkcyjnych.
Po szeroko zakrojonych poszukiwaniach firma zwróciła się do Graphite Additive Manufacturing Ltd, pozyskując rozwiązanie HP Jet Fusion 4200 Industrial 3D.
Wyzwanie
Kluczowym wyzwaniem dla Eagle E-Types był problem małego wolumenu elementów. Firma tworzy jedynie cztery lub pięć modeli E-Type w ciągu roku. Poza tym, istnieje pięć wariantów tego modelu, z kierownicą po lewej lub prawej stronie. Każdy model ma zupełnie inną specyfikację techniczną.
Z tego względu firma stosuje pewne zindywidualizowane części w bardzo małych ilościach – niekiedy jedną na rok. Normalne metody produkcji, takie jak wycinanie laserowe, obróbka i formowanie wymagają wytwarzania większych ilości, aby zachować ekonomiczną opłacalność.
Firma Eagle E-Types musiała znaleźć sposób na tańsze wytwarzanie części, z których wiele przeznaczonych było do wnętrza samochodów, gdzie są widoczne dla kierowcy. Jednak najważniejsza wciąż była jakość. Każdy element tych odrestaurowanych, klasycznych aut musiał wyglądać idealnie i być taki w dotyku.
Rozwiązanie
Przez ostatnie cztery lata firma Eagle ściśle współpracowała z Graphite Additive Manufacturing Ltd., brytyjskim biurem usług druku 3D, wytwarzającym pojedyncze modele lub serie produkcyjne elementów funkcjonalnych dla firm.
Aby rozwiązać problem, Eagle E-Types i Graphite Additive Manufacturing sięgnęły po HP Jet Fusion 4200 Industrial 3D. Zaprojektowane do wytwarzania najwyższej jakości, funkcjonalnych części – do prototypowania i produkcji – to rozwiązanie drukowania 3D zapewnia usprawnione, wydajne i efektywne doświadczenie produkcyjne.
Jest też wysoce konfigurowalne i pozwala wytwarzać małe serie produkcyjne bez zaporowych kosztów ogólnych tradycyjnych technologii. W dodatku tam, gdzie w przypadku poprzedniej technologii firma Graphite Additive Manufacturing Ltd. musiała ręcznie mieszać materiały i ładować maszynę, HP Jet Fusion 3D 4200 usprawnia przepływ pracy dzięki systemom automatycznego mieszania materiałów I załadunku.
W firmie Graphite Additive Manufacturing Ltd., technologia HP pomogła skrócić cały dzień pracy do zaledwie 30 minut. Dzięki zwiększonej automatyzacji, technologia HP pozwoliła Graphite Additive Manufacturing Ltd. zredukować zużycie materiałów podczas produkcji, dzięki możliwości odzyskania i ponownego użycia nadmiarowego materiału.
Wynik
Elementy drukowane trójwymiarowo HP umożliwiają Eagle ekonomiczne zamawianie pojedynczych części, gdyż cyfrowy model 3D można łatwo dostosować i wydrukować ostateczną część. Oznacza to, że w razie potrzeby każda część może stanowić ewolucję poprzedniej, bez dodatkowych kosztów wynikających ze zmiany innej niż wysyłka.
Od chwili zastosowania technologii HP Jet Fusion 3D 4200 do wytwarzania przewodów klimatyzacji i ogrzewania w samochodach E-Type, firma Eagle odnotowała znaczący spadek czasów oczekiwania, usprawnienie procesów oraz większą elastyczność w zakresie spełniania szczególnych żądań klientów.
„Byliśmy pod wrażeniem tego, jak bardzo poprawił się wygląd części wydrukowanych z HP 3D, oraz ich trwałości” – powiedział Paul Brace, dyrektor Eagle. “Przewody ogrzewania musiały wyglądać wystarczająco atrakcyjnie, aby umieścić je na desce rozdzielczej, a te części pasują do wyjątkowej jakości naszych klasycznych aut. Dzięki technologii HP po raz pierwszy osiągnęliśmy żądany poziom wykończenia.
Dodatkowe zalety, jakie zauważyliśmy, to szerszy zakres kształtów, które możemy teraz wytwarzać w drukarkach 3D, oraz redukcja wagi oferowanych materiałów. Zapewnia to wartość dodaną dla klientów, którzy chcą jak najbardziej zmniejszać wagę części”.
„Jesteśmy zachwyceni, że indywidualizacja oferowania przez technologię HP umożliwia Eagle elastyczność i wydajność podczas projektowania wiodących na rynku pojazdów na zamówienie. Możliwość zastosowania druku 3D do wytwarzania wysokiej jakości części samochodowych zapewnia wiele rozwiązań dla sektora motoryzacyjnego i ekscytuje nas myśl, jak wpłynie na kształtowanie produkcji samochodów w nadchodzących latach” – mówi George Brasher, Dyrektor Zarządzający UK&I w HP.
HP Jet Fusion 3D 4200 oferuje klientom łatwe w użyciu rozwiązanie, którego skala zmienia się wraz z działalnością, a także zintegrowany, całościowy proces zapewniający zarówno funkcjonalne prototypy, jak i części końcowe.
Do pobrania: