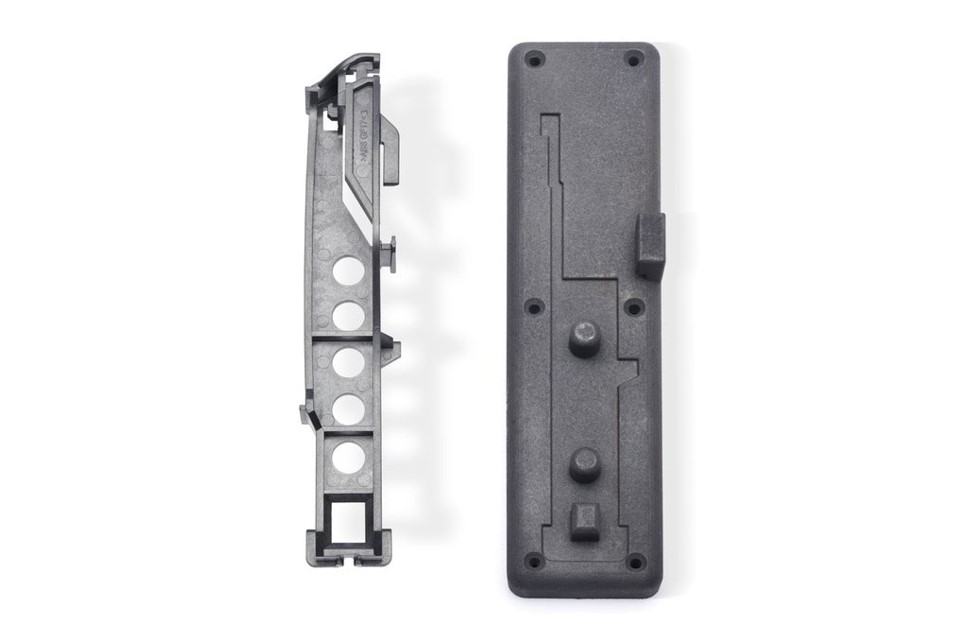
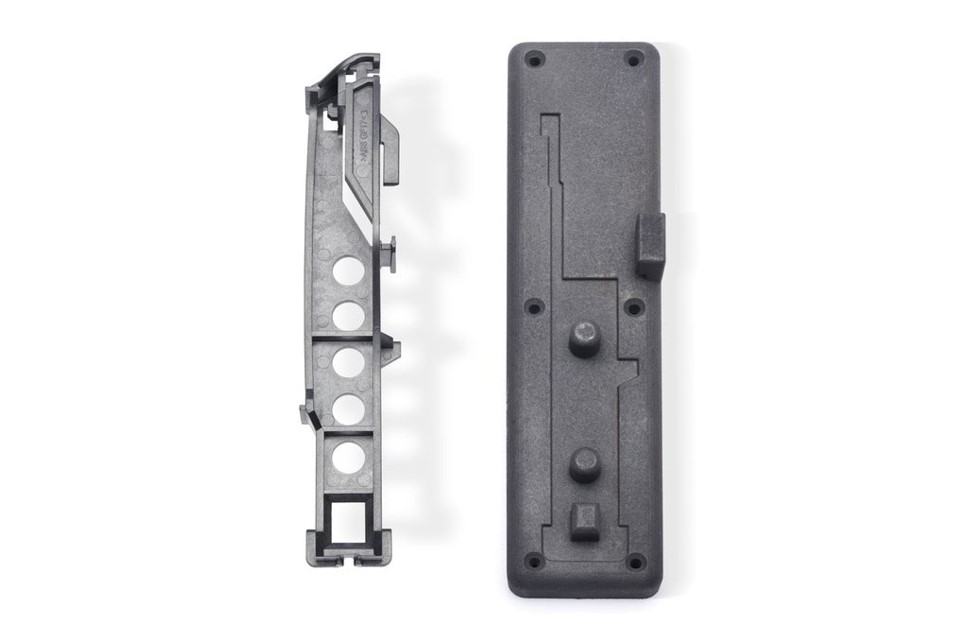
Aereco wdraża technologię HP Multi Jet Fusion na różnych etapach cyklu powstawania przyrządów i uchwytów produkcyjnych.
Wstęp
Aereco opracowuje rozwiązania wentylacyjne dla budynków mieszkalnych i biurowych z modulacją przepływu powietrza dostosowaną do indywidualnych potrzeb. Zastosowane technologie umożliwiają tworzenie produktów dostosowanych do wymagań wydajności energetycznej i jakości powietrza w budynkach.
Grupa Aereco założona w 1984 r. w Marne la Vallée (Francja) obsługuje klientów w ponad 30 krajach. Obecnie zatrudnia ponad 450 pracowników.
Aktualnie zespoły Aereco badają, projektują i prowadzą testy z wykorzystaniem innowacyjnych narzędzi i produktów. Firma zaczęła stosować przemysłowy druk 3D w celu usprawnienia procesów produkcyjnych i szybszego opracowywania prototypów.
- Branża
Przemysłowa - Sektor
Ogrzewanie, wentylacja i klimatyzacja - Technologia | Rozwiązanie
Technologia HP Multi Jet Fusion (MJF), drukarka 3D HP Jet Fusion 4200 - Materiał
HP 3D High Reusability PA1 12
Przyrządy, uchwyty produkcyjne i oprzyrządowanie – Stanowisko montażowe
Linia montażowa, stanowiąca największą strefę w fabryce Aereco zarządzana jest przez Specjalny Zespół Maszynowy, który zapewnia prawidłowe funkcjonowanie linii i pracuje nad optymalizacją różnych stanowisk montażowych. Każde ze stanowisk może być obsługiwane przez jedną lub większą liczbę osób. Każda z nich wyposażona jest we wszystkie niezbędne narzędzia, przyrządy, uchwyty produkcyjne, maszyny, elementy oraz części niezbędne do realizacji każdego z etapów montażu.
Podczas awarii przyrządu, uchwytu produkcyjnego lub oprzyrządowania na linii montażowej, firma Aereco niejednokrotnie była konfrontowana z brakiem części zamiennych oraz możliwości szybkiego ich wytworzenia. Inżynierowie potrzebowali technologii, która pomoże im w przystępny kosztowo sposób rozwiązywać tego typu problemy i tym samym skrócić czas przestojów produkcyjnych.
Nicolas Muris, kierownik ds. Projektów w Aereco, uznał, że konieczne jest wprowadzenie zmian na stanowiskach montażowych i postanowił sprawdzić, czy druk 3D można wykorzystać do produkcji części.
W tym celu Muris zastąpił wszystkie elementy frezowane, płytę nośną oraz obudowy bezpieczeństwa częściami wykonanymi w technologii druku 3D HP Multi Jet Fusion (MJF). Wytwarzanie przyrostowe wykorzystał również do produkcji części, takich jak zindywidualizowane elastyczne połączenia, tace zaciskowe wbudowane w płytę oraz oszczędny system regulacji głębokości przycisków.
Wytwarzanie części dla stanowiska roboczego za pomocą technologii druku 3D HP MJF pozwoliło firmie zmniejszyć koszty operacyjne o 90%, z 3.000 € (w przypadku aluminium i stali nierdzewnej) do 300 € (w przypadku HP Multi Jet Fusion i HP 3D HR PA 12).
Usprawniony, dzięki HP MJF, proces produkcji umożliwił wytwarzanie bardziej złożonych części takich jak regulowane przyciski rozruchowe oraz poprawił komfort i zwiększył wydajność pracowników.
„W najnowszych projektach stacji montażowych wprowadzamy elementy spersonalizowane, które każdy pracownik może dostosować tak, aby zapewnić sobie większą wygodę” – powiedział Muris.
Swoboda projektowania, jaką zapewnia technologia HP Multi Jet Fusion sprawiła, że firma Aereco mogła przeprojektować zautomatyzowany montaż na stanowiskach i połączyć trzy różne etapy w jeden. Dzięki właściwościom mechanicznym materiału HP 3D HR PA 12 stanowiska są lżejsze i bardziej wytrzymałe od tych zaprojektowanych konwencjonalnie.
Prototypowanie – pokrywa wywiewu wentylacyjnego
Przed rozpoczęciem produkcji inżynierowie Aereco opracowują prototypy w celu walidacji projektów i zbadania funkcjonalności. Tworzenie prototypów tradycyjnymi technologiami było w przeszłości bardzo kosztowne, gdyż wymagało od inżynierów modyfikowania formy w przypadku każdej iteracji projektu. Dzięki technologii HP Multi Jet Fusion, proces prototypowania, czas i koszt uległy znacznemu skróceniu.
„Jak zawsze w przypadku badania i rozwoju produktów, najważniejszym czynnikiem na etapie rozwoju i prototypowania jest czas wprowadzenia produktu na rynek” – mówi Pierre Kraus, Menadżer w Aereco.
Aby spersonalizować uchwyt ścienny wyciągu powietrza poprzez dodanie logotypu klienta, firma Aereco mogła wykonać wiele iteracji projektu tego małoseryjnego elementu bez konieczności stosowania kosztownych metalowych form. Stworzenie prototypu tradycyjnymi metodami zajmowało nawet 2-3 tygodnie, ale obecnie dzięki technologii HP Multi Jet Fusion Aereco realizuje całość w ciągu dwóch cykli druku, co trwa jedynie 4 dni.
„Technologia HP Multi Jet Fusion nie tylko umożliwia na łatwiejsze i szybsze tworzenie prototypów, ale też pozwala od samego początku procesu produkcyjnego myśleć o sposobach opracowania zoptymalizowanego projektu produktu, lżejszych części i uproszonego montażu” – powiedział Kraus.
Część końcowa – zasuwa wywiewu wentylacyjnego
Wywiewy można konstruować tak, aby spełniać konkretne wymagania, które są typowe dla danego rodzaju budynku (np. użyteczności publicznej, przemysłowe, mieszkalne itp.). Każdy z nich bowiem podlega innym wymaganiom dotyczącym jakości powietrza, takim jak zakres wilgotności, natężenie przepływu, czy poziomy CO2.
Zasuwę wywiewu Aereco trzeba było przeprojektować pod kątem zapewnienia zgodności z tymi przepisami. Inżynierowie Aereco wykorzystali technologię HP MJF oraz podstawowy projekt, który zmodyfikowano. Aby wykonać jedną z adaptacji dostosowano siłownik, a konkretnie mały element wewnętrzny skrzydełek żaluzji wywiewu.
„Początkowo rozważaliśmy wytworzenie części w drodze formowania wtryskowego, ale po wykonaniu obliczeń zdaliśmy sobie sprawę, że dla średniej partii produkcyjnej musielibyśmy wytworzyć jedynie 300 jednostek rocznie w okresie 3 lat” – opowiada Thomas Bourgois, inżynier Aereco. “Opcja formowania wtryskowego była zbyt droga, nie uzasadniała kosztu modyfikacji lub stworzenia metalowych form i nie zapewniała zwrotu z inwestycji. Dlatego zdecydowaliśmy się na wytworzenie części w technologii HP Multi Jet Fusion, która daje nam znacznie większe możliwości oraz elastyczność we wdrażaniu małych i szybkich zmian w celu dodatkowych adaptacji produktu, jednocześnie redukując koszt wytwarzania poszczególnych elementów”.
W przypadku formowania wtryskowego, koszt jednej części wynosi 0,11€, więc dla 300 części rocznie w okresie 3 lat koszt wyniósłby 99€ plus 4 000€ za przeróbki metalowej formy. Ostatecznie koszt formowania wtryskowego wyniósłby w sumie 4033€. W przypadku HP Multi Jet Fusion, koszt wynosi 0.28€ za część, czyli całkowity koszt 300 części rocznie przez 3 lata wyniesie 252€, co daje różnicę 3.847€ i redukuje koszt o 94%.
1. Drukarka 3D HP Jet Fusion 3D przy użyciu materiału HP 3D High Reusability PA 12 zapewnia współczynnik ponownego wykorzystania nadwyżki proszku na poziomie 80% podczas produkcji części funkcjonalnych. Do celów testowania materiał jest poddawany procesowi starzenia się w rzeczywistych warunkach drukowania i jest śledzony według generacji (najgorszy przypadek do ponownego użycia). Następnie z każdej generacji wytwarzane są części i poddawane testom pod kątem właściwości mechanicznych i dokładności.