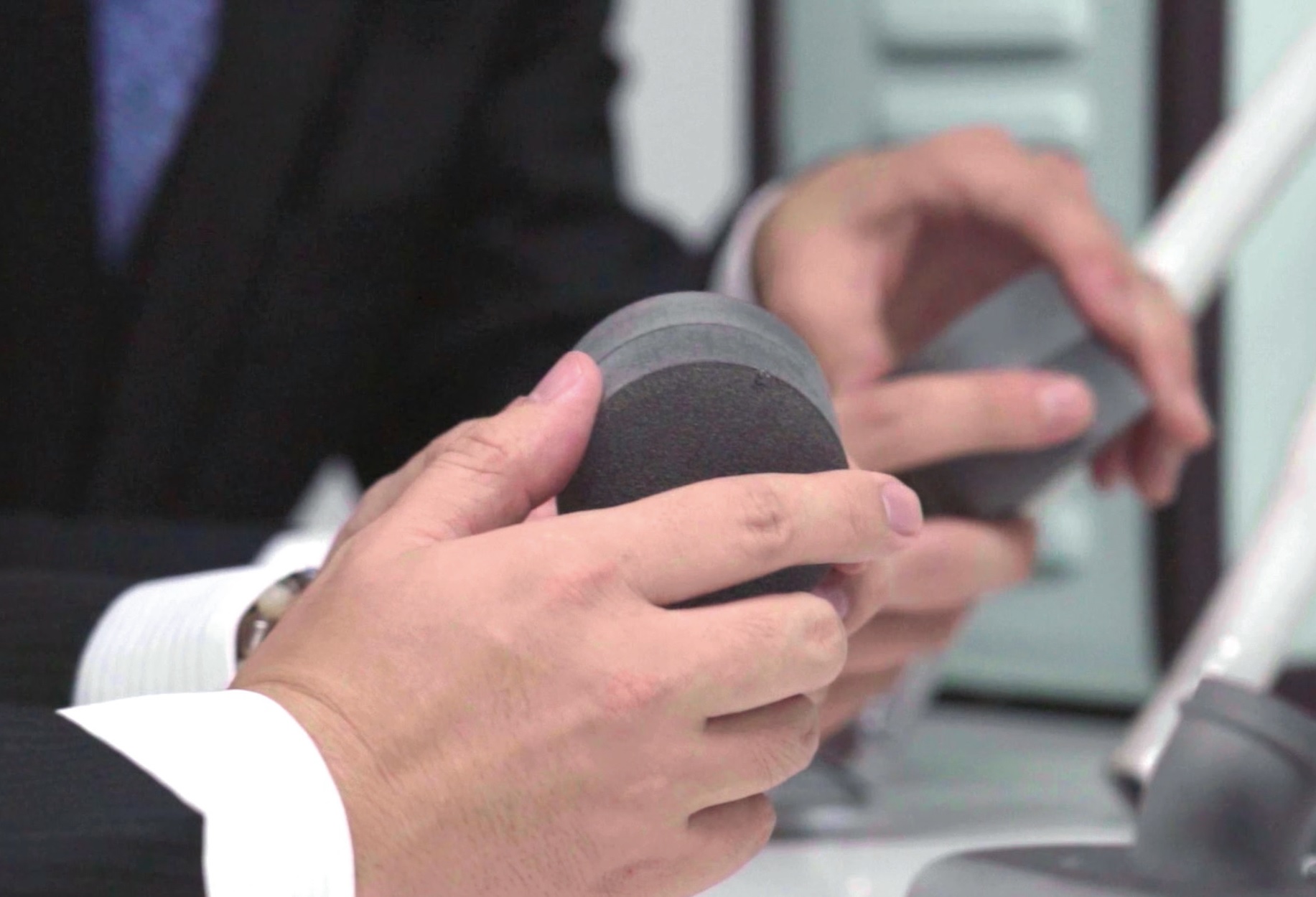
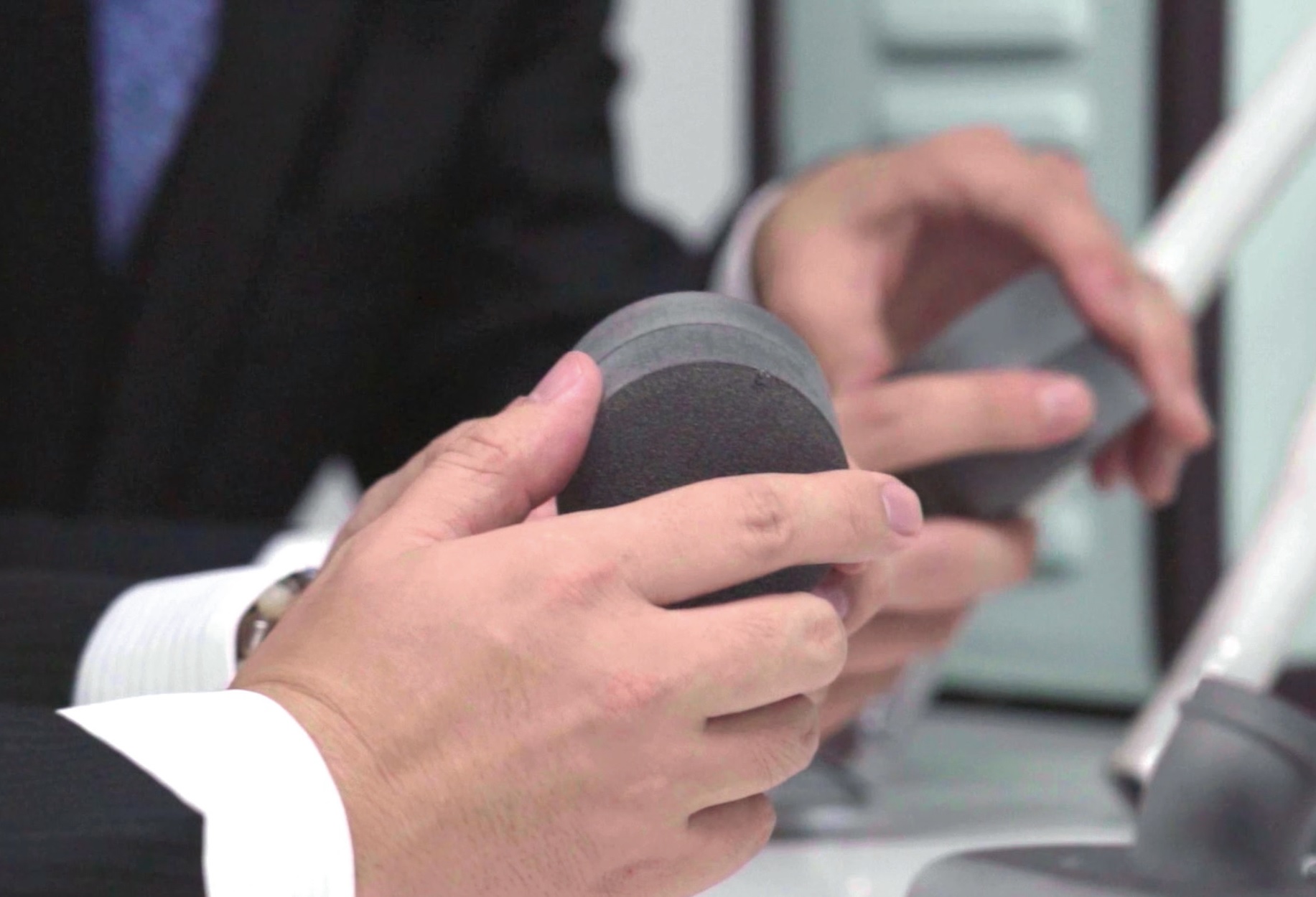
Streszczenie
Największą wartość w przypadku produkcji addytywnej osiąga się, gdy druk 3D jest wprowadzany na bardzo wczesnych etapach cyklu życia produktu. To na tych etapach projektanci mogą rozpatrywać projekty, które są możliwe tylko dzięki wytwarzaniu addytywnemu, redukcji liczby złożeń i optymalizacji projektów pod kątem konkretnego procesu produkcyjnego. Rola, jaką projekt 3D odgrywa w tym procesie, zmienia się w zależności od tego, na jakim etapie cyklu rozwoju znajduje się produkt.
Wprowadzenie druku 3D do cyklu rozwoju
Il. 1: Wartość produkcji addytywnej w cyklu rozwojowym.
W wielu przypadkach jednak łatwiej jest rozpocząć proces adaptacji od istniejącego produktu. W niniejszym artykule przedstawiono kilka metod automatycznej optymalizacji projektu, które mogą pomóc w pełnym wykorzystaniu możliwości produkcji addytywnej podczas transformacji produkcji z tradycyjnych metod wytwarzania na takie, które wykorzystują technologię HP Multi Jet Fusion (MJF) dla elementów, które zostały już zaprojektowane.
Drzewka decyzyjne dotyczące przeprojektowania przedstawione w tym artykule pomogą zespołom określić elementy, które mogą być wydrukowane z zastosowaniem technologii 3D i ocenić rekomendowaną strategię przeprojektowania dla każdej z nich. Czynniki, które wpływają na tę decyzję, to m.in. masa elementu, jego wielkość, oczekiwany wolumen produkcji oraz wymagania mechaniczne.
Istnieją trzy strategie przeprojektowywania, które mogą być stosowane, gdy część została już zaprojektowana dla innej metody wytwarzania: hollowing [puste w środku] wewnętrzne struktury kratownicowe i optymalizacja topologiczna.
Duże, masywne elementy są świetnymi kandydatami do zastosowania strategii przeprojektowania.
Biorąc pod uwagę niewielką inwestycję czasową wymaganą do zastosowania przeprojektowania, obróbki elementów z niepełnym wypełnieniem lub stworzenia wewnętrznych struktur kratownicowe, osiąga się dużą redukcję wagi/kosztów w stosunku do zainwestowanego czasu na przeprojektowanie. Jednak strategie te mogą być stosowane tylko do gęstych elementów.
Struktury lekkie kratownicowe są stosowane, gdy masywne elementy wymagają wysokiej wytrzymałości mechanicznej, ale jednocześnie dają bardzo podobną redukcję kosztów jak elementy niewypełnione całkowicie [hollowing], co czyni je godną polecenia strategią przeprojektowania w celu utrzymania wystarczających właściwości mechanicznych i uzyskania wysokiej redukcji kosztów.
Metody optymalizacji topologicznej zapewniają najbardziej optymalną redukcję kosztów/wagi przy jednoczesnej maksymalizacji parametrów mechanicznych elementów, ale wymagają znacznie większych nakładów czasowych.
Dla cienkich elementów, optymalizacja topologiczna lub ręczna zmiana projektu są jedynymi strategiami przeprojektowania, które mogą być użyte, a inwestycja czasowa musi być uzasadniona wielkością produkcji (przypadek biznesowy) lub wzrostem wydajności, który może być uzyskany.
Grubości ścianki mniejsze niż 2 do 2,5 mm nie są zalecane przy technologii hollowing (modeli pustych w środku). Zalecana grubość ścianki będzie zależeć od konkretnej funkcji i wielkości każdego elementu i będzie wymagać przetestowania.
Aby osiągnąć optymalną równowagę pomiędzy redukcją kosztów/wagi a parametrami mechanicznymi, zalecaną geometrią jest ostrosłup oparty na formie ostrosłupa o podstawie sześciościanu (geometria 3) o wielkości komórki 8 mm i grubości belki 1,2 mm.
Chociaż nie ma ograniczeń drukowania dla analizowanych parametrów (tj. w pełni wypełnionych elementów), rozsądnie jest przeprojektować części, aby osiągnąć najlepszą jakość elementów i i zmaksymalizować spójność i powtarzalność produkcji. Wydajność podczas drukowania masywnych elementów może być ograniczona przez limit gęstości upakowania modeli w komorze roboczej. Tak więc, te strategie przeprojektowania pomogą również zmaksymalizować produktywność Twojej drukarki 3D.
KOMPONENTY PUSTE W ŚRODKU [HOLLOW] [Il. 2a]
- Szczególnie nadaje się do masywnych elementów, które nie wykazują wysokich wymagań mechanicznych.
- Automatyczne przeprojektowanie, które można zastosować w ciągu kilku minut. Koszty i waga bardzo zredukowane.
STRUKTURY KRATOWNICOWE [LATICCE] [Il. 2b]
- Szczególnie nadaje się do masywnych elementów, które wymagają właściwości mechanicznych.
- Automatyczne przeprojektowanie, które może być zastosowane w ciągu kilku minut, gdy tylko wymagany jest pewien styl struktury dla specyficznego elementu.
OPTYMALIZACJA TOPOLOGICZNA [Il. 2c]
- Szczególnie przydatna do cienkich elementów lub elementów o złożonym rozkładzie obciążeń.
- Nakłady czasu na przeprojektowanie są wyższe i wymagają więcej godzin pracy inżynierów.
- Zoptymalizowana redukcja wagi jest osiągana dzięki obliczeniowej naturze procesu, przy jednoczesnej maksymalizacji właściwości mechanicznych części.
Il. 2: Główne cechy trzech strategii przeprojektowywania.
Ocena elementów
Zaczynając od listy potencjalnych kandydatów, poniższy schemat pomoże zdecydować, które elementy mogą w pierwszej kolejności podlegać przeprojektowaniu. Trzy kluczowe aspekty, które należy wziąć pod uwagę to:
- Konstrukcja elementu: W przypadku bardzo litych elementów, potencjalna redukcja wagi i kosztów jest bardzo istotna przy korzystaniu ze swobody projektowania druku 3D, i dlatego są to najbardziej odpowiednie elementy, do których można zastosować strategie przeprojektowania przedstawione powyżej. Jeśli chodzi o elementy, które nie są masywne, dwie pierwsze strategie przeprojektowania nie mają zastosowania, a czas zainwestowany w zastosowanie strategii optymalizacji topologicznej musi być uzasadniony innymi parametrami, takimi jak rozmiar elementów lub wielkość produkcji.
- Rozmiar elementu: Zmniejszenie kosztu i wagi o dany procent zawsze będzie miało większe znaczenie bezwzględne dla dużych elementów, zarówno pod względem kosztów, jak i wzrostu wydajności (niższa waga). W przypadku małych elementów, wpływ zmiany musi być oceniony w kategoriach wielkości produkcji, aby uzasadnić czas zainwestowany w przeprojektowanie.
- Wielkość produkcji: Duży wolumen produkcji może sprawić, że przeprojektowanie z niższym kosztem/redukcją wagi będzie miało istotny wpływ i dlatego w takich przypadkach ocenie należy poddać aspekty ponownego projektowania.
Poniższe drzewo decyzyjne zapewnia systematyczne podejście do podejmowania decyzji, które elementy powinny zostać przeprojektowane.
Strategie przeprojektowywania
Elementy niewypełnione
Zaletą tej metody jest to, że przeprojektowanie trwa bardzo krótko i jest proste, oraz że może znacznie zmniejszyć masę części. Jednocześnie może również niestety zredukować właściwości mechaniczne do tego stopnia, że dany element nie będzie już spełniać stawianych wymagań. Dlatego elementy lite, które nie mają wysokich wymagań mechanicznych są świetnymi kandydatami do tej strategii przeprojektowania.
Ogólnie rzecz biorąc, części o grubości większej niż 15 mm można uznać za części lite, chociaż analiza powinna być przeprowadzana indywidualnie dla każdego przypadku.
Il. 4: Proces drążenia elementu krok po kroku.
Ogólnie rzecz biorąc, minimalna zalecana grubość ścianki to 2 mm, ale w przypadku dużych elementów, grubość 2,5 mm będzie skutkować lepszą wydajnością. Konieczne jest określenie optymalnej wartości z uwzględnieniem charakterystyki danego przypadku. Zalecamy rozważenie konstrukcji kratownicowej gdy wymagana grubość ścianki w celu spełnienia wymagań funkcjonalnych przekracza 15 mm.
Stosując tę strategię przeprojektowania, redukcja kosztów jest osiągana poprzez użycie mniejszej ilości proszku, biorąc pod uwagę mniejszą powierzchnię do stapiania, a zatem stapiana jest mniejsza liczba proszku, co może pozwolić na większą gęstość upakowania, a zatem większą liczbę części w ramach konstrukcji. Przykładowo, podczas redukcji wypełnienia tych kostek, zużycie stosowanego proszku zostało zredukowane o około 80%.
Struktury Kratownicowe
Metoda ta polega na wydrążeniu elementu i i zastąpieniu litej masy obszaru wewnątrz niej strukturami kratownicowymi. Zaletą tej metody w porównaniu do zwykłego drążenia elementu jest to, że zachowuje ona większość właściwości mechanicznych oryginalnej części litej, przy jednoczesnym zmniejszeniu jej masy, a tym samym kosztów. Ponadto, przeprojektowanie jest szybkim procesem, który może być zautomatyzowany, ale redukcja kosztów i wagi nie jest tak znacząca jak w przypadku poprzedniej metody.
Il. 5: Część lita i część o strukturze lattice.
Istnieją dwa parametry, dzięki którym projektanci mogą dostroić się do wymagań mechanicznych elementu do przeprojektowania: grubość ścianki oraz rodzaj zastosowanej konstrukcji kratownicowej.
Aby wybrać odpowiedni typ struktury, należy uwzględnić trzy parametry:
- Geometria: Geometria każdej komórki siatki definiuje rozkład obciążenia. Geometrie elementów kratownicowych mogą być izotropowe lub anizotropowe. Pozwala to projektantowi na wprowadzenie różnych właściwości lokalnych do końcowej części, w zależności od jej pożądanej wydajności.
- Rozkład punktów lub wielkość komórki: Rozkład punktów określa wielkość każdej komórki elementu: Im większy rozmiar komórki dla danej geometrii, tym mniejsza liczba komórek potrzebna do uzyskania tej samej objętości, a tym samym większa redukcja wagi/kosztów, ale również większa redukcja właściwości mechanicznych.
- Grubość belki: Im grubsze belki w strukturze kratownicowej, tym lepsze właściwości mechaniczne, ale tym mniejsza redukcja kosztów/wagi.
Wielkość komórki (mm) | ||||||
Grubość belki (mm) | 0.8 | 1 | 1.2 | 0.8 | 1 | 1.2 |
Zmniejszenie objętości | 89% | 62% | 47% | 87% | 84% | 82% |
Odkształcenie przy ściskaniu | ŚREDNIE | NISKIE | NISKIE | WYSOKIE | ŚREDNIE | ŚREDNIE |
Wielkość komórki (mm) | ||||||
Grubość belki (mm) | 0.8 | 1 | 1.2 | 0.8 | 1 | 1.2 |
Zmniejszenie objętości | 86% | 78% | 69% | 86% | 83% | 80% |
Odkształcenie przy ściskaniu | ŚREDNIE | NISKIE | NISKIE | WYSOKIE | ŚREDNIE | ŚREDNIE |
W związku z tym, biorąc pod uwagę redukcję masy i właściwości mechaniczne badanych geometrii, zalecamy zastosowanie geometrii piramidy typu heksahedronu (Geometria 2) o wielkości komórki 8 mm i grubości belki 1,2 mm jako ogólny wymiar struktury kratownicowej, który powinien być zastosowany. Jednakże, każda część musi być badana indywidualnie, aby określić typ struktury, która lepiej spełni wymagania danego elementu.
Jeśli chodzi o redukcję kosztów osiąganą podczas stosowania wewnętrznych struktur wypełnienia, zastosowanie takiego działania zwykle zmniejsza koszty o 60% do 70%. Tak więc, struktury tego typu są zalecanym przeprojektowaniem dla elementów pełnych, ponieważ możliwe jest osiągnięcie lepszych parametrów mechanicznych przy bardzo podobnej redukcji kosztów w porównaniu z elementami pustymi w środku.
Poniższa tabela i wykres porównują jakościowo trzy strategie przeprojektowania w oparciu o kryteria opisane na początku rozdziału.
Kryteria / Strategia przeprojektowania | Puste w środku [Hollow] | Wewn. struktury kratownicowe | Optymalizacje topologiczne |
Obniżenie kosztów produkcji | Duże | Duże | Bardzo duże |
Czas potrzebny na optymalizację projektu | Kilka minut | Kilka minut | Godziny |
Wiedza na temat wydajności części | Podstawowa | Podstawowa | Duża |
Wymagania SW | Zarządzanie CAD lub STL | Zarządzanie CAD lub STL | CAD + FEM |
Redukcja wagi | Duża – bardzo duża (w zależności od tego, czy niestopiony proszek znajduje się w środku czy nie) | Średnia | Bardzo duża |
Tabela 2: Podsumowanie różnych metod przeprojektowania.
Il. 6: Wykres porównujący różne atrybuty każdej strategii przeprojektowania.
Strategie przeprojektowania
Jeśli chodzi o elementy, które warto przeprojektować, są cztery kluczowe aspekty które pomogą wybrać najlepszą strategię:
- Właściwości mechaniczne: Strategie pustych w środku elementów typu hollow najprawdopodobniej nie będą odpowiednie, jeśli elementy muszą być odporne na naprężenia mechaniczne. Dlatego ważne jest, aby od początku zrozumieć potrzebę (lub jej brak) tych wymagań.
- Złożoność działania: Złożoność działania odnosi się do złożoności obciążeń działających na dany element i dlatego dotyczy tylko tych części, które w pierwszej kolejności wymagają określonych właściwości mechanicznych. W przypadkach, w których rozkład obciążeń jest prosty, stosowanie strategii optymalizacji topologicznej nie zawsze ma sens, ponieważ ręczne przeprojektowanie lub automatyczna struktura kratownicowa mogą być jeszcze łatwiejsze i szybsze do zastosowania oraz mogą skutkować tym samym poziomem redukcji kosztów/wagi. Każdy przypadek wymaga jednak analizy. Optymalizacja topologii jest zalecana, gdy złożoność elementu jest taka, że dla projektanta nie jest proste znalezienie najlepszej metody przeprojektowania.
- Elementy lite: Czasami to, na ile element jest lity, określa zalecaną metodę przeprojektowania. W przypadku bardzo gęstych, litych elementów, zastosowanie struktur wewnętrznych kratownicowych lub metody niepełnego wypełnienia, przyniesie najlepszą redukcję kosztów/wagi, ale nie będzie miało sensu zastosowanie tych metod, jeśli elementy nie są masywne. W takich przypadkach, ręczne przeprojektowanie lub optymalizacja topologiczna są najlepszymi strategiami przeprojektowania.
- Wielkość produkcji: Czas zainwestowany w przeprojektowanie elementów musi być uzasadniony w drodze analizy danego przypadku biznesowego. Dlatego ważne jest, aby wziąć pod uwagę również ten parametr przy wyborze strategii przeprojektowania.
Poniższe drzewko decyzyjne pomoże zdecydować, która strategia przeprojektowania jest najlepsza dla danego typu części.
Il. 7: Drzewo decyzyjne do podejmowania decyzji o najlepiej dopasowanej strategii przeprojektowania dla każdego typu części.
Do pobrania: